Home
Take your business to the next level, become remarkable with local innovation.
Our country is filled with remarkable people and remarkable ideas. At the Department of Science and Innovation, we help businesses turn ideas into action by enabling local health innovation to grow our health industry while meeting the needs of society.
Happenings
Keep up to date with the latest ecosystem events and opportunities.
Our Partners
The Innovation Bridge Portal is an initiative of the South African National Departments of Science & Innovation (DSI), and Small Business Development (DSBD). The initiative is supported by the European Union (EU) and its content does not necessarily reflect the views of the EU.
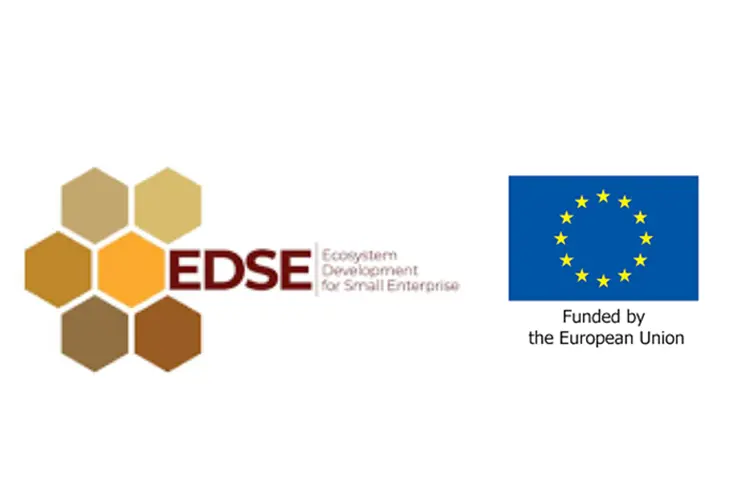
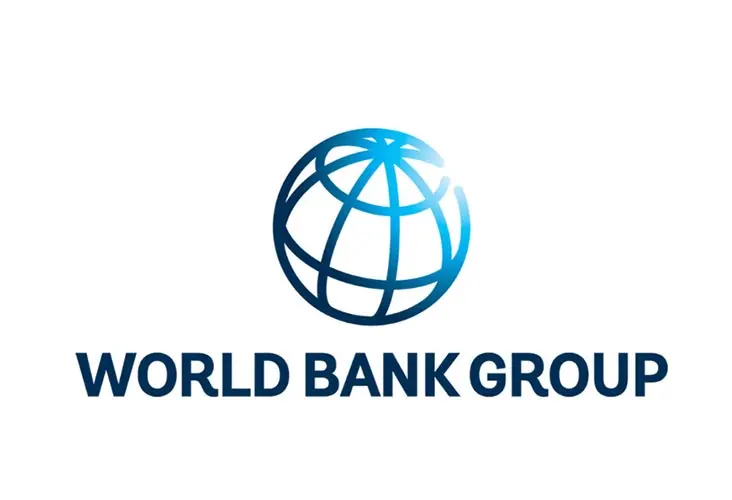
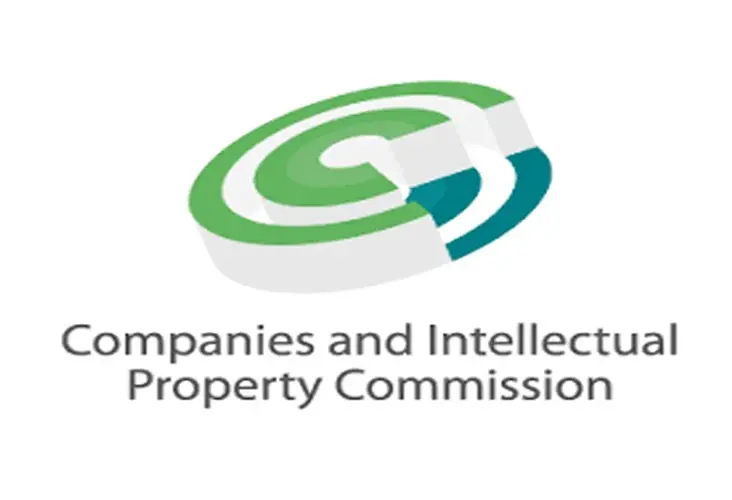
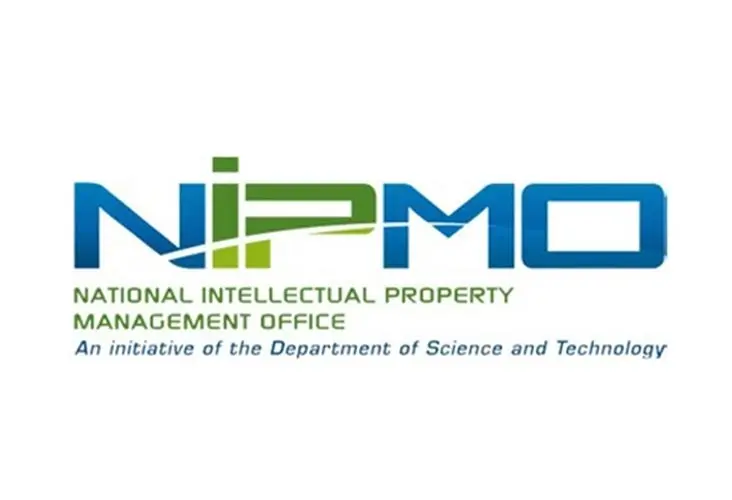