Circular Economy in SA: Renewing Plastic Waste with the DSI
In recent years, the global production and consumption of plastics have experienced unprecedented growth. From 1950 to 2015, plastic production skyrocketed nearly 200-fold, reaching a staggering 381 million tonnes annually.
While per capita plastic consumption in African countries remains relatively low, projections indicate a significant surge in plastic imports for key nations such as Egypt, Nigeria, South Africa, Algeria, Morocco and Tunisia.
By 2030, these countries are expected to double their plastic imports, with an estimated 165 million tonnes of plastics reaching end-of-life across African nations in the coming decade.
The current linear "take-make-waste" plastics economy poses substantial challenges, both environmentally and socially. Low-income and vulnerable communities often bear the brunt of these negative impacts.
Plastic waste infiltrating our oceans jeopardises food security and economic development, while unmanaged waste on land can contribute to the spread of diseases like malaria and Ebola.
It's clear that plastic pollution isn't merely an environmental concern – it's a major socio-economic and development challenge that requires innovative solutions. A comprehensive circular economy approach to plastics emerges as the only viable solution capable of addressing the scale of this problem.
To tackle packaging waste specifically, three key strategies have been identified:
- Elimination: This involves finding innovative ways to design out unnecessary packaging or develop solutions that render packaging obsolete.
- Reuse business models: These models keep packaging in circulation for multiple cycles, either through return systems or customer refill programmes.
- Material circulation: This strategy focuses on redesigning packaging to ensure it can be effectively recycled or composted.
By implementing these strategies, we can maximise the economic, societal and environmental benefits of plastics while minimising – and eventually eliminating – their negative impacts, source.
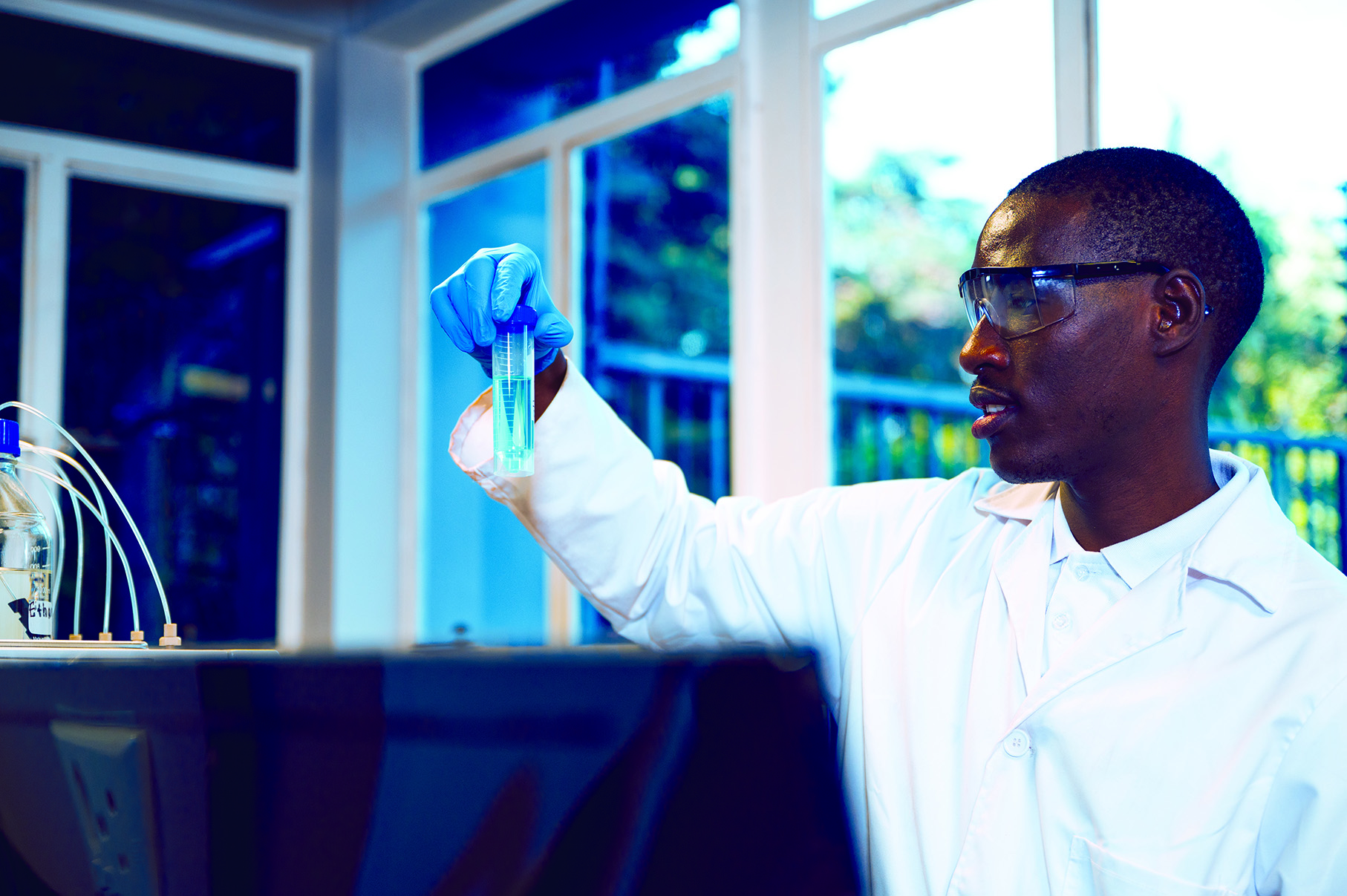
Turning plastic waste into sustainable energy: a game-changer for South Africa
While the idea of burning plastic might seem counterintuitive, recent innovations have revealed its potential as a sustainable fuel source. Plastic waste, with its high content of hydrogen and carbon, possesses an energy content comparable to refined fossil fuels like diesel.
This characteristic, combined with the abundance and constant production of plastic waste, positions it as a reliable and potentially inexhaustible energy source.
What makes this approach particularly appealing is its versatility – all forms of plastic waste, from grocery bags and food containers to bottles and cling film, can be utilised as fuel. This presents a significant opportunity for countries like South Africa, where excess plastic waste often ends up in landfills.
The potential for a thriving plastic circular economy in South Africa is substantial. Despite boasting some of the highest recycling rates globally, the country still grapples with an abundance of plastic litter.
By collecting and recovering this waste for energy production, South Africa can address two pressing issues simultaneously: sustainable energy generation and job creation.
This represents an opportunity to innovate, create new revenue streams and contribute to solving a critical environmental challenge.
By investing in plastic-to-energy technologies, companies can position themselves at the forefront of sustainable practices while potentially tapping into new markets and government incentives, source.
Understanding the plastic-to-fuel process: a technological overview
To fully grasp the potential of plastic-to-fuel technology, it's essential to understand the process. Here's a breakdown of the key stages:
- Collection and sorting: The process begins with the collection of plastic waste from various sources such as households, industries and recycling centres. This material is then meticulously sorted to remove any non-plastic contaminants.
- Shredding and pre-treatment: The sorted plastic is shredded into small pieces to increase surface area and improve process efficiency. Additional pre-treatment steps, such as washing or drying, may be employed to remove contaminants like dirt or moisture.
- Pyrolysis: This is the core of the process. The shredded plastic undergoes thermal decomposition at high temperatures (typically 300°-500°C) in an oxygen-free environment. This breaks down the plastic into simpler hydrocarbon molecules.
- Vaporisation and condensation: The vapours produced during pyrolysis are cooled and condensed into a liquid containing various hydrocarbon compounds and impurities.
- Refining: The condensed liquid undergoes further processing, including fractional distillation and hydro-processing, to separate and purify different hydrocarbon fractions. This results in usable fuels such as gasoline, diesel and kerosene.
- By-product handling: Any by-products generated during the process, such as char or residue, are treated through additional processes like hydro-cracking, or are recycled or disposed of appropriately.
- Gasification: An alternative to pyrolysis, gasification involves reacting plastic waste with a gasifying agent (steam, oxygen or air) at high temperatures (500°–1300°C). This produces synthesis gas, or syngas, which can be used to generate electricity through fuel cells.
The compelling advantages of converting plastic waste into fuel
The excitement surrounding plastic-to-fuel technology is well-founded, with many envisioning landfills as the oil fields of the future. The advantages of this technology are numerous and significant:
- Environmental benefits: The fuels produced through this process have properties of clean fuel, resulting in a lower carbon footprint compared to coal, oil and natural gas when burned.
- Circular resource utilisation: By using existing carbon and hydrogen molecules, this process reduces the need for new carbon extraction, aligning with circular economy principles.
- Reduced incineration: Converting plastic to fuel decreases the amount of plastic incinerated, thereby reducing associated carbon emissions.
- Landfill diversion: This technology prevents hard-to-recycle or non-recyclable materials from ending up in landfills, addressing a critical waste management challenge in South Africa.
- Versatility: There's potential to expand this method to include other waste materials, including those that may not be easily recyclable, such as metal waste.
- Industrial application: The chemical compounds produced can replace fossil fuel-based alternatives in existing production lines, offering a more sustainable option for various industries.
- Cost-effectiveness: Once the initial plant setup is complete, the operational costs are relatively low, making it an attractive long-term investment.
- Reduced methane pollution: By decreasing reliance on traditional oil and gas production, which is associated with significant methane pollution, this technology contributes to reducing greenhouse gas emissions.
These advantages represent not just environmental benefits, but also potential competitive edges in an increasingly sustainability-focused global market, source.
UNISA's disruptive technologies: pioneering solutions for environmental challenges
The University of South Africa (UNISA) is at the forefront of developing innovative solutions to address societal challenges while protecting the environment. Their work in plastic waste management and energy generation is particularly noteworthy.
The University of South Africa (UNISA) has developed an energy-generating system that utilises polyethylene plastics to produce synthesis gas (syngas). What sets this system apart is its anaerobic gasification process, which eliminates the need for oxygen and removes the air separation step.
This innovation significantly lowers energy costs compared to conventional gasification systems.
Key features of the University of South Africa’s (UNISA) system include:
- Anaerobic gasification: This unique approach simplifies the process and reduces energy requirements.
- Latent heat recovery: The system can recover a portion of the latent heat of water, leading to improved energy production compared to conventional designs.
- Polyethylene plastic feedstock: By using this common plastic waste as feedstock, the system addresses a major environmental concern.
The benefits of this system are substantial:
- Higher energy production: The simplified gasification process and heat recovery lead to increased energy output.
- Low energy costs: The elimination of the air separation step results in significant energy savings.
- Efficient plastic waste disposal: The system provides an effective method for disposing of plastic waste while generating valuable energy.
The University of South Africa’s (UNISA) innovation presents opportunities for collaboration, technology transfer, and potential commercialisation, source.
How the DSI supports local innovations and how you can get involved
Recognising the pressing need to transition towards a more circular economy that minimises waste and environmental harm, we are prioritising funding, research support and the promotion of local innovations in conversion technologies that support a circular economy approach.
By reducing pollution, conserving resources, and deriving economic value from materials that would otherwise be discarded as environmental hazards, the Department of Science and Innovation (DSI) supports initiatives that offer immense potential for benefiting industry, agriculture, communities and the environment.
Final Thoughts
In conclusion, the circular economy approach to managing plastic waste in South Africa offers a transformative path forward. By rethinking the “take-make-waste" model and embracing innovative circular economy technologies like plastic-to-fuel conversion and sustainable energy generation, South Africa can create new economic opportunities.
The efforts of institutions like UNISA and the support of the DSI highlight the nation's commitment to pioneering circular economy solutions that benefit both the environment and society.
To find out more about accessing these circular technology innovations or to engage with the UNISA, visit DSI today.
DSI, making sure it’s possible.